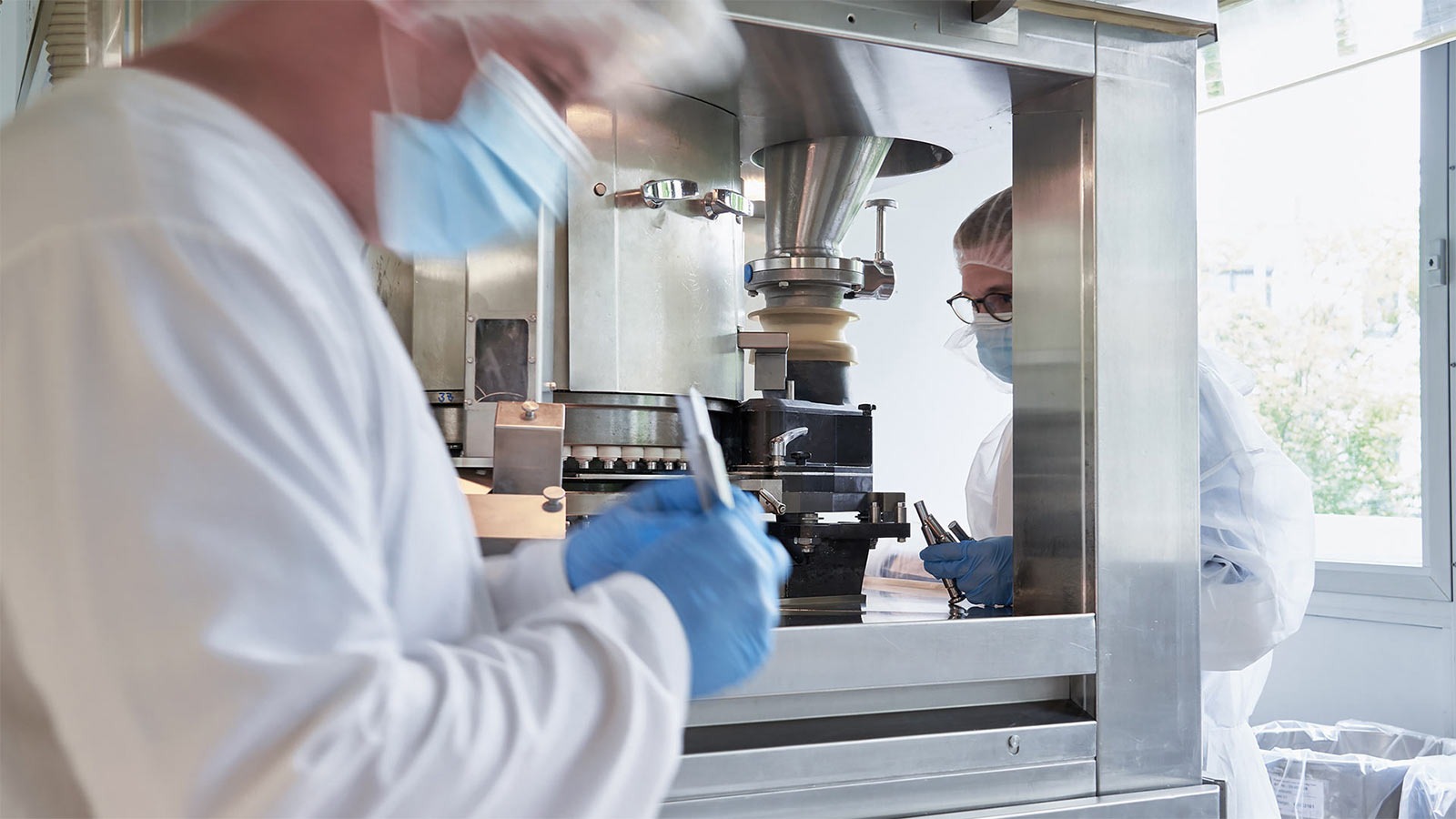
On the basis of “Lifetime Efficiency”, Fette Compacting supports companies along the entire life cycle of machines. The importance of this type of cooperation is indicated by the example of bene-Arzneimittel GmbH, a German contract and own product manufacturer in Munich. During the production of a special painkiller tablet, the goal was to optimize the product quality in an effort to continue to comply with the company’s high requirements.
bene-Arzneimittel specializes in products featuring paracetamol which it offers in numerous forms and dosages. The variant featuring additional codeine – as a supplementary analgesic – concerns a formula which has been used for many years, but this combination also makes it a complex formulation. The newly established “Pharmaceutical Technology” department at bene-Arzneimittel chose this process and the particular formulation for systematically exploring optimization possibilities. Many tablets containing codeine feature the active agent in granulate form which increases the costs of raw materials and products. In contrast to its competitors, codeine is pressed directly at bene-Arzneimittel. This permits more cost-efficient production but also requires the corresponding process expertise. In view of the potential of the tried-and-tested formulations, this process expertise is to be optimized on a step-by-step basis. In order to utilize all of the available levers in the downstream process of tableting, bene-Arzneimittel turned to the performance consultants at Fette Compacting for support.
A sensitive mix
First of all, the aim was to take a close look at the various factors influencing the pre-process. “Building on this, we developed a concept for changes to the mixing process in order to have their influences on tableting systematically analyzed by Fette Compacting,” claims Tobias Werum, who is a validation specialist in the Pharmaceutical Technology department at bene-Arzneimittel. Adjusting these levers swiftly led to an improved mixing quality and flow properties as well as more consistent filling of the tablet press for the subsequent tableting process.
Even minor adjustments can have major impacts on tablet quality: quality control at bene-Arzneimittel
Optimal parameters and the right tools
“On the basis of initial results, we were able to further improve the result by adjusting the machine,” explains Jochen G?th, a performance consultant at Fette Compacting who assessed the individual changes and their influence on tableting. This enabled the number of bad tablets to be reduced by around 50 percent. In an effort to prevent flaking on the top side of the tablets, additional parameter adjustments were made. “By changing the immersion depth, we achieved better ventilation and were able to improve the quality once again,” is how G?th describes one of the main levers he succeeded in identifying during the tests conducted in collaboration with Tobias Werum. Consequently, there are plans for long-term optimization of the tools used. For example, investments in new segments and an improved Fill-o-Matic are to ensure optimized ventilation in the future.
A close partnership
Employees in the Pharmaceutical Technology department at bene-Arzneimittel act as technological experts, providing in-house and – in the case of contract jobs – external consulting with the requisite know-how on the optimization potential of the respective production facility. On a partnership basis, this cooperation between the performance consultants at Fette Compacting and the experts in the Pharmaceutical Technology department ultimately led to an improved mixing quality thanks to the joint expertise available for this project, as well as very good flow properties, optimized and consistent tableting, and specific investments for continuous improvement. All in all, this cooperation enabled a more than three-fold increase in output to 180,000 tablets per hour – accompanied by improved tablet quality.
bene-Arzneimittel was extremely satisfied with the result: “We can also apply the current results and optimizations to other product groups, thereby continuously improving the performance of our products,” adds Werum.
Efficiency for an optimal process
Without any complex new formulation, the team collaborated in finding a significantly simpler solution which also ensures an optimized overall process. In view of the good results, further improvements are planned to extend the optimized process and product quality as well as to further increase output – while reducing the number of bad tablets.
“Lifetime Efficiency is a comprehensive and continuous process,” explains Jochen G?th. “It starts with an analysis of the production requirements and conditions in our Technology Center and continues along the entire life cycle of the machines. Our experience has shown that practically every process harbors some potential. And it is our goal to lever this potential.”
Would you like to take a closer look at your production?
Talk to our Performance Consultants
E-Mail: Consulting@fette-compacting.com